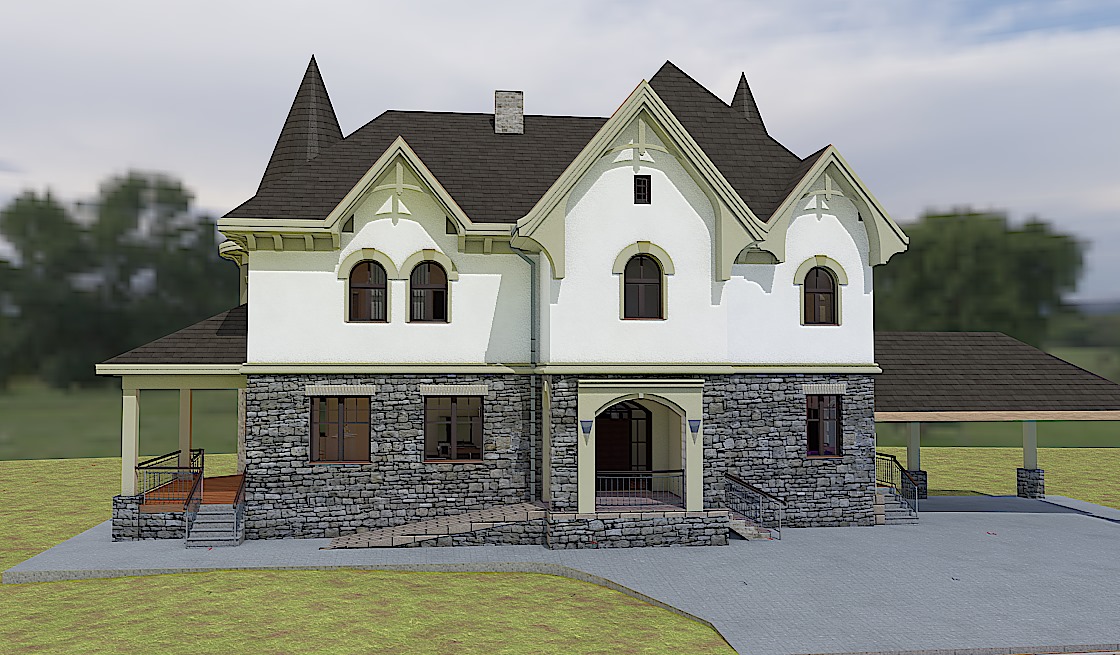
I had just finished a design for a two-story castle-style house, and already before I started the design, I could see the problems that would be encountered during the construction of the house because the clients insisted on gas-block walls. As you can see in the picture, the house has two round towers adjacent to spacious rooms with large spans.
The first problem is the round towers.
If you build with large-format blocks like aerated concrete, as the customers wanted, you would have to say too much aerated concrete to perfectly fit the blocks without using cement mortar, which significantly reduces thermal efficiency. Sawing narrow pieces out of any material is difficult. So what is the solution? I suggested building the towers out of monolithic concrete with permanent polystyrene foam formwork. However, the builders refused to build using this technology and persuaded the customers to build towers out of brick.
Advantages of building custom walls from monolithic concrete.
The concrete takes the shape you specify. It would help if you had a radius or curved wall - make a suitable formwork. For individual construction of curved walls, conventional plywood formwork is not suitable - it will be too expensive to make, but it is economically justified for large objects. In addition, removing the formwork is also costly.
When building a private home is best to use permanent formwork. There are many kinds of permanent formwork, but the radius walls are the best-suited EPS (polystyrene foam). Even with straight blocks can be made radius formwork. You only need to make a few cuts in each block and then give the necessary shape.
FOR INFORMATION: 1 SQUARE METER OF INSULATED AND SHEATHED FRAME WALL COSTS 900 RUBLES, OF AERATED CONCRETE 1900 RUBLES, AND A MONOLITHIC STRAIGHT WALL ABOUT 1300 RUBLES. THE PRICES ARE FOR WALLS WITH APPROXIMATELY THE SAME THERMAL EFFICIENCY.
However, these prices do not yet determine the cost of the finished house. There are many more nuances, which I will mention next.
My customers have already chosen a foreman who will build the house. Supervisors like to put on an intelligent face and deflect uncomfortable decisions away from them, especially since this particular foreman was not from outside. He has never built by this technology, and he does not want to learn - he does not want to take risks - he needs to make money, not save customers' money.
In general, we decided to build a wall of brick, which is not at all sensible. I will explain why.
For a two-story house with high ceilings carrying capacity of the wall with a similar thickness to gas-block (380 mm) is not enough - you need to build a wall with a thickness of 510 mm. At the same time, customers were limited in the length of the house. The house will be placed strictly against the 3-meter line from the fence of the neighbors. Therefore, the area of rooms inside the towers decreased. During construction, there will be problems with the joint of the brick wall and aerated concrete wall - it is on the drawing to connect the lines, and try to connect the aerated concrete with brickwork - without the "crutches" will not work: have to use reinforcement and mesh. It would be better to build the whole house from brick. However, this is just the beginning of the problems.
The second problem is a slab span of more than 6 meters.
Both rooms adjacent to the towers have a large span. However, if in one room the monolithic slab is not a problem, in the living room, the slab will carry a piece of the outer wall and a couple of partitions! Even though the part of the tower's outer wall that stands on the slab is a little less than a meter and a half long, its weight, together with the roof and snow load, is about 4 tons. Simple solutions will not work here. Another problem appears in both towers: the high conical roof needs something to lean on, and the future owners want an open space without columns and retaining walls. Of course, technically, it is solvable, but at what cost?
If the house were built with frame technology, there would be no problem - installing trusses instead of boards will solve the problem. That is why our site has so many beautiful American house projects with intricate multi-pin roofs, towers, and skylights. A-frame house is lightweight - to solve similar problems somewhere, we use trusses and a large section of timber with no rebar, mesh, and other overheads.
If the house were built with ICF technology, the problems would be minimal. Walls, slabs, transoms, and beams are connected by reinforcement into a single frame and, together with the concrete and formwork, become a solid building. It is true that moving the walls or changing the location of a window or door will be problematic.
I do not understand what you think when you build a house out of aerated concrete. The roof - frame, the floor, the foundation, lintels, armored belt - monolithic, inside the walls - reinforcement. Why such complications? I would understand if the house had at least one advantage over the construction of other materials. However, an aerated concrete house has almost none. Let us look at the most significant advantages of any house.
Advantages of different house designs
- The most arduous house is a cast-in-place concrete or brick house.
- The warmest house - monolithic concrete or frame house.
- The most inexpensive house - frame, timber, or log house.
- The fastest house - frame and monolithic concrete.
- The most accessible house to change is a frame house.
- Quietest house - brick, concrete with fixed formwork and frame house with eco wool and gypsum or cement-bonded particleboard.
- The most environmentally friendly house is a frame house (the others are far from environmentally friendly).
- The most technologically advanced house, where it is easiest to lay wires and pipes - a frame house.
- The most fire-safe house is a brick, concrete, or aerated concrete with no roof or furniture.
One conditional advantage. Fire safety of the frame of the house. Moreover, for the sake of this advantage, do you want to build a house of aerated concrete? Another thing is a frame house.
A-frame house is the warmest, least expensive, quickest to build, easy to change, quietest, most environmentally friendly, and technologically advanced.
When sellers of aerated concrete talk about strength, they give figures for structural cellular concrete with a density of D800 or higher. The same when they talk about soundproofing. When they talk about thermal efficiency, they give block grade D400, which has soundproofing and strength less than any other building material. People who bought apartments in houses built on the technology of cast-in-concrete frame with aerated concrete filling complain of neighbors snoring and noise from passing cars near the house. Seriously.
Why build aerated concrete walls to put rebar inside and over the walls to do reinforcement belt of concrete and think then this reinforcement belt to insulate? Isn't it easier to start building the armored belt from ground zero and lead up to the top of the floor? However, some people do not like simplicity; they need to overcome difficulties. Then they get satisfaction; they feel like heroes.
And then you still have to puzzle: how to conduct the pipes in the walls or how to hang a heavy kitchen cabinet on the wall. If you want a stone house, then build a monolithic one.
MONOLITHIC CONCRETE HOUSE WITH PERMANENT FORMWORK - THE STRONGEST, WARMEST, QUICKEST, QUIETEST, MOST FIREPROOF (WHEN USING CHIP-CEMENT BOARDS FOR THE INNER FORMWORK) AND RELATIVELY INEXPENSIVE.
The third problem is the difficulty of building a roof.
In most houses - roofs frame; only in modern houses with a flat roof can they be monolithic? However, sometimes do a monolithic gable roof if the house is a simple rectangular shape and, accordingly, a simple roof.
The problem is the connection of structures made of different materials—the easiest way to build a roof in a frame house. And understandably so. It is the same design; just the roof boards are placed obliquely. In other houses, the roof must be connected to the walls. To do this, a Mauer last is used. I do not know where the word came from in the Russian language, but it sounds worse than lashes. This is done on purpose so that "non-builders" do not understand anything. Mauerlat is a board or bar attached to the wall and then to the rafters - a bar or planks. In a frame house, there is no Mauer last. The rafters are attached directly to the walls, reducing the number of construction operations. This is one of the reasons why the frame houses are inexpensive - not because of low quality, but because of high technology and simplicity. Everything brilliant is simple.
So how do you tie a mauerlage to a masonry wall?
The easiest thing to do in a monolithic house. It is enough to embed the anchor bolts in the wet concrete at regular intervals. Then string a bar on them and tighten the nuts. You can run a wire or steel band under the top reinforcement. You will not be able to immure the anchor bolt into the brick walls, but you can lay pieces of long wire or steel bands 5-6 rows before the top of the wall. These tapes should be long enough to be able to girdle the bar and nail it in place. The wire is simply twisted, but this is not the most reliable method - the strength of the wire is not high - it is made of mild steel.
With foam blocks or aerated concrete, everything is much more complicated. It is possible to make strokes (grooves) along the walls, in which to lay reinforcement and wire or steel tape, and under the rafters to put a wide steel strip to distribute the load from the rafters. However, a concrete belt with a laid reinforcement cage is again poured on top of the wall more often. Then, at the same time, with the reinforcing frame, anchor bolts or studs are installed in it. This reinforcement belt is made half the width of the wall, but in some cases, such as with this house, the reinforcement belt will be made for the entire width of the wall. The roof is so complex and high - two more stories will fit in the attic. A reliable reinforcement belt must carry such a mega.
In other words, it seems simple. However, think about it. In a house of aerated concrete to finish the wall at a certain height, build the formwork, tie the armature in the frame, pour concrete, wait until the strength is gained, remove the formwork, install the outer blocks or insulation, and only then lay the Mauer last. This is the most difficult attaching mauerlatta compared to other structures. Another thing to remember is that the meerkat of the attic roof should be higher than the ceiling at least half a meter - for laying a good layer of insulation. If you do not want to freeze, the average strip should insulate the ceiling with a layer of insulation thickness of 400 mm, and in colder climates and more. Attic wall is also needed to inspect the walls and roof, so you can crawl up to the rafters since it is the bottom of the rafters most often exposed to destruction from rotting.
The fourth problem is the foundation.
Yes, on the one hand, aerated concrete uses less concrete when building walls. However, on the other hand, because of its width and fragility, it requires a more robust and broader foundation than is necessary for wood and concrete houses.
Wood is flexible. Concrete is brittle - they put rebar in the concrete to improve flexibility. Even with foundation problems, these houses will not form serious cracks and are unlikely to collapse. Aerated concrete and foam concrete are other matters. Their modulus of elasticity is six times less than wood and 12 times less than steel (reinforcement holds the walls).
However, this is also not the biggest problem. For a frame and monolithic concrete house, a strip foundation is only 20 or 25 cm thick. After all, the thickness of the foundation walls is determined by the thickness of the supporting walls, despite the high load-bearing capacity of the concrete foundation. Walls that are 400 mm thick need a foundation that is the same or thicker. At the same time, the frost penetration depth is the same for walls of any thickness.
Note that the agitators of building a house from aerated concrete, when they talk about the cost of the box, never mention the cost of the foundation, as if tacitly letting you know that the cost of the foundation for all houses is the same and depends only on the area of development.
If we calculate the cost of 1 sq.m. wall of aerated concrete, it will be much cheaper than the house walls with permanent concrete formwork. A paradox? No. You need to count 1 meter from the foundation to the roof. That is when you see the difference. The average cost of 1 sq.m. monolithic concrete wall in 2019 is about 1300 rubles, and the wall of aerated concrete is 1900 rubles. At the same time to erect monolithic walls is much easier and faster, and the net area of the house will be higher with the exact exterior dimensions.
If you count only the cost of the foundation walls, the house of cast concrete with a basement will cost the same as the house of aerated concrete without a basement. A basement is a necessary thing; if not immediately, then later will be helpful. Many are afraid to build a basement for fear of flooding. However, this fear is based on old construction methods, when bricks or concrete blocks were built. With monolithic construction and modern waterproofing materials, the presence of drainage pipes, this unpleasantness is minimized.
The fifth problem is the laying of utilities.
A house is not a house if it does not have water and electricity. It is necessary to install electrical and water mains, sewerage, and heating in the house. In the past, most houses were built of brick or logs. Moreover, in one or the other construction to lay any network covertly - a big problem. Therefore, in older two-story houses, they tried to put the kitchen and bathroom in the same place, sacrificing the convenience of the layout. In modern houses made of brick, log, and aerated concrete do the same. Sometimes another riser is added.
In this home project, one second-floor bathroom was initially placed over the first-floor bathroom. However, the house turned out to be too long for the purchased plot and expensive. So we had to shorten the house by 2 meters by moving the bathrooms elsewhere. We had to break our heads with the location of risers and change the layout of bathrooms by technical capabilities rather than with the convenience of future tenants.
Installation of cables in houses made of brick and aerated concrete is time-consuming because it is necessary to drill through the walls and fill the seams. You can lay most of the networks inside the formwork in cast-in-place concrete houses before the concrete is poured. If something is missing, you can cut chinks in the fixed formwork, which is easier than foam concrete.
There are no such problems in a frame house - everything is laid inside the frame of the walls or floor. Hence the high speed of construction of frame houses.
Let us summarize
We looked at five problems when building a house with aerated concrete. These are not all problems. The other problems will appear later in the operation of the house. This is dampness caused by the high hygroscopicity of aerated concrete and the cracking of plaster on the interior walls because of the "breathing" walls. By the way, the walls should not breathe; they are not alive. The walls should be airtight so that together with air and moisture does not leave the heat. After 20 years, the pipes may fall into disrepair cracks or cracks at the joints. How will you fix them if they are under the foundation slab?
To avoid these problems, choose a house construction that has been tested by time, studied by builders on the experience of millions of houses. Among these designs, there are no houses made of aerated concrete or foam blocks. Aerated concrete houses have only been built for 30 years and only in a few countries globally—tens of thousands versus a few million. Remember, sellers, do not benefit from your well-being.