Few people know that a wooden floor is healthier than a concrete slab. If you think of building a house with a wooden floor, you have made the right choice. The wooden floor is built in homes with walls of brick, aerated concrete blocks, monolithic concrete, and, of course, in houses made of logs, beams, and frame houses. It would help if you decided what building materials are best suited for you.
In general, there is not much choice - lumber, LVL beam, I-beams, and wooden trusses. All of these materials are in a different price range. If the critical point in choosing a building material is cost, do not rush to use the cheapest material. After all, it may turn out that you can save more on something else by buying more expensive building material.
Let's try to find out what are the secrets behind building material used for floor construction.
What's hiding inside the floor?
Plumbing and drainage
A house is more than just a foundation, walls, and roof. Electrical wires, water, and sewer pipes, heating and ventilation pipes run throughout the house. If you want to build a comfortable home, you need to place the rooms to move around the house comfortably, not the builders who will be installing pipes, wires, ventilation, etc. Therefore, often the upstairs bathrooms are not vertically aligned with the downstairs bathrooms. It means that it may be necessary to run some of the sewer and water pipes inside the floor to conceal them to the riser.
Some people think you can't do that because of the risk of leaks. But their experience is based on the outdated equipment of older homes, built when the choice of materials for installing plumbing and sewage was severely limited. There is a wealth of worldwide experience in laying utilities in walls and ceilings in today's reality. If the builders perform their work qualitatively, using modern plastic or metal pipes, seals, and waterproofing, the risk of leaks is almost zero, but the convenience of using the bathroom adjacent to the bedroom you will enjoy every day.
Ventilation
Another element of comfortable living in a house is ventilation. Following the codes, all rooms must be adequately ventilated. These rules have existed for a long time, but designers usually provide only one ventilation shaft per apartment when designing apartments. Ventilation is provided only in the kitchen and sanitary facilities. But in your own home, especially if it is large enough, such ventilation will not be enough, especially when we strive to make our house warm, carefully closing all air passages to keep warm.
Ask people who have had their bedrooms vented how they sleep and how they feel. Sleeping outdoors, even in winter, will protect you from many diseases. So you need to make ventilation throughout the house. It is possible if the builders can lay some of the HVAC inside the ceiling.
Wiring
Let's also remember about electricity. In most homes, it's hard to find a room that doesn't have ceiling lights. But it might be easier (and more economical for you) to run the electrical inside the ceiling and wire for other installation devices. It's usually more convenient and safer to run the cables in fireproof plastic or metal pipes.
In concrete and brick houses with reinforced concrete floor slabs, all these utilities are usually hidden in ducts and rarely in walls or inside the floor. Unlike a concrete floor slab, a wood floor is a great place to put wires and pipes. Therefore, it is worth considering the floor as a load-bearing structure and as a box for laying wires.
Which is better? Lumber boards, I-beams, or trusses?
According to the code, the floors for sleeping rooms are designed for less load. Therefore the distance between the joists can be larger, and most often, you should install joists at two feet distance between the axes. On the lower floor, this distance is usually 16 inches, sometimes even 12". Most often, the floor builders use at least 2x8 joists. (See tables of cross-sections of beams and spacing for bedrooms and attics).
The wood joist floor is the cheapest, but also less practical:
- Because the wood tends to dry out and curl.
- It is tough to find perfectly straight lumber.
- It is challenging to find lumber more than 200 mm wide, which may need to overlap a greater span.
As shown in the table for the residential area, the maximum span for a 2x8 joist is 14 feet. When building modern houses with an open floor plan, the joist length may not be enough to cover the span. To break up the span, you will have to install intermediate beams, which also increases the cost and reduces the height of the ceiling. Of course, you can leave planed beams in plain sight as a decorative element.
Lumber
The problem with the floor of planks is something else.
For ventilation, builders lay 4" to 8" ductworks. These ducts just won't fit in the floor space.
- The HVAC will not always run parallel to the joists.
- With the small thickness of the floor will be impossible to pull such ducts.
- You can make holes or cuts in the boards, but not in the outer thirds between the supports, but only in the middle and relatively small. Therefore, inside a wooden floor of this thickness, builders only lay wires, water, or heating pipes.
They install ductwork and sewer pipes only a short distance without crossing the joists.
Wooden I-beams
I-beams have several advantages over timber boards: the span is longer, they do not dry out or twist, and they are perfectly flat, and you can buy beams with a larger cross-section. I-joists are usually made in the mill. The top and bottom chords are made of dry planed wood or LVL, with plywood or OSB between them. It is not allowed to saw or chamfer the wooden chords, as this is where the most significant stress is exerted. In this case, the greatest load acts on the outermost parts of the beams near the supports (walls). Drill holes or make rectangular cut-outs in the middle part of plywood or OSB beams. See figure for a diagram of the technological holes.
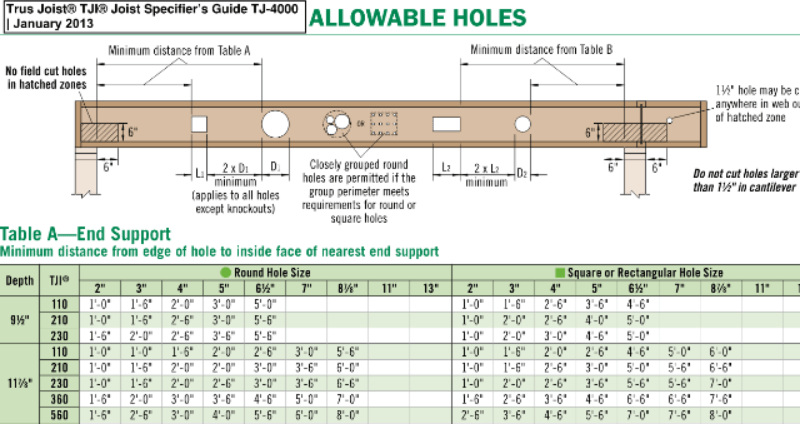
Caution: Drilling, sawing, sanding produce wood dust. I-beam paint and/or protective coatings may contain titanium dioxide. Wood dust and titanium dioxide can cause cancer. Use respiratory protection when working.
The disadvantage of I-beams is that you have to do a lot of drilling or sawing of rectangular holes to run pipes of different diameters. It takes quite a lot of time. Besides, I-beams are afraid of moisture, so you need to protect them from precipitation during construction. The advantage of I-beams compared to trusses is their lower cost and no need to order them in advance.
Wooden and combined floor trusses
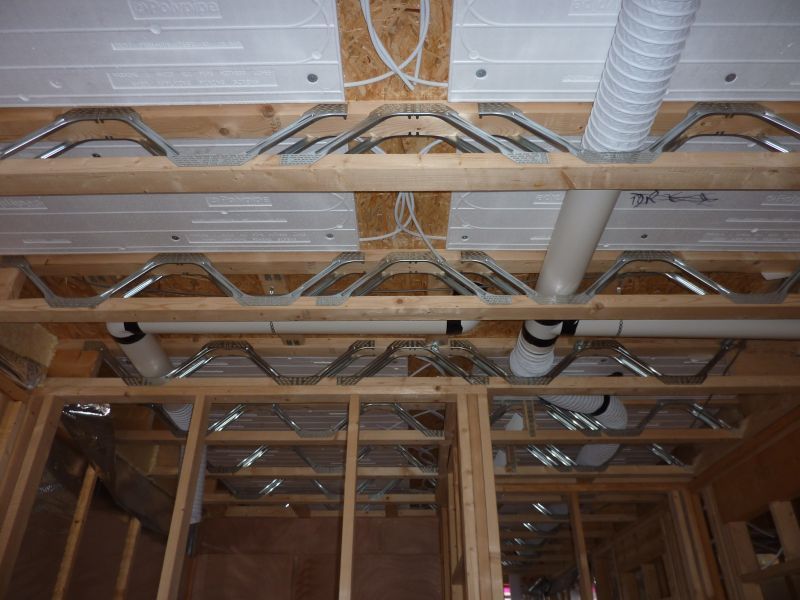
Unlike I-beams, trusses are made of natural materials and do not have to have holes in them. Thanks to their lattice structure, ductwork can be passed through them in any direction without much difficulty. Wooden trusses are usually made to be at least 1 foot wide, allowing ductwork to pass through them. Wooden trusses can span up to 30 feet (sometimes more), have perfect geometry, and not dry out or twist.
But the cost of wooden trusses is relatively high. Also, it is necessary to order them in advance because for each house, the design of the truss is calculated individually. The difference in cost between plank flooring and trusses to cover 1,000 square feet can exceed $2,000. But this difference is only in the cost of the material. If you consider the cost of laying communications, the cost of additional pipes, wires, which will have to be laid along a longer path, can compensate for this difference. Besides, you may need to do additional wiring or heating in the future, and in the event of a significant renovation, wood trusses can help cut the cost of these jobs significantly. Wood trusses are also almost twice as expensive as wood I-beams; natural products almost always cost more. But, as with the boards, it saves a lot of time laying utilities. The amount of work you can judge by the photo below, which shows only part of the floor of a small house in terms of area, shows how many large and small holes the craftsman had to make.
Conclusions
From all of the above, we can conclude that when building a house with a larger area of two floors (or with a basement floor), wooden trusses are preferable to other building materials for the floor frame. Especially when you consider that, in principle, wooden trusses can be made by yourself, although you will have to tinker, and if you are not a specialist, it will be necessary to order the calculation to an engineer who owns a specialized program for the analysis of trusses.
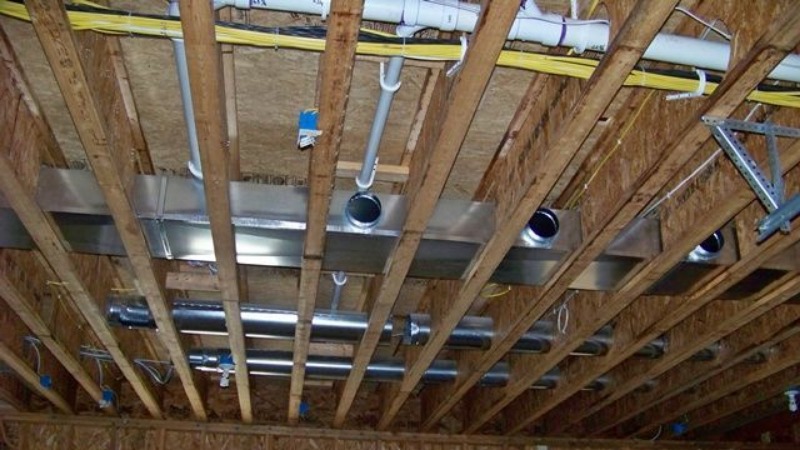