A table of heat conductivity of building materials, their density, and specific heat capacity of materials in the dry state at atmospheric pressure and temperature of 20...50°С is given (if no other temperature is specified).
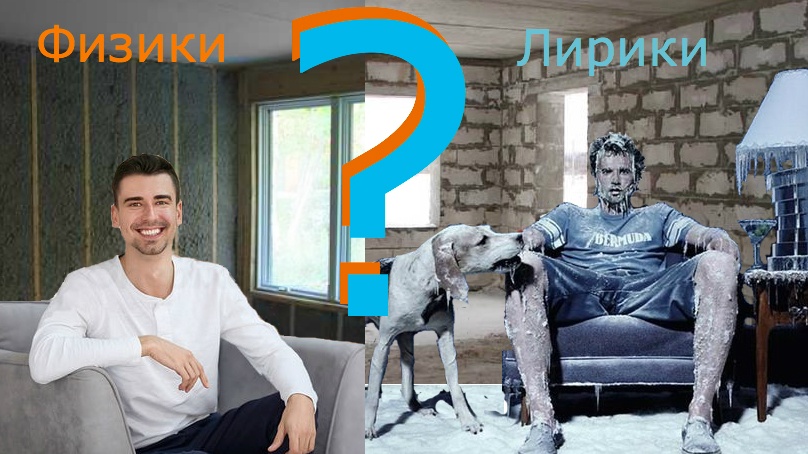
Note the thermal conductivity of building materials in the table. There is no linear relationship between thermal conductivity and density. In the table, some materials with lower density have higher thermal conductivity and vice versa. Not all materials with low thermal conductivity can be used in home insulation. Some building materials can make the health of home occupants worse, such as glass wool, which because of the short length of the fibers, penetrates cracks and eventually ends up in the lungs, which can lead to asthma or lung cancer. We have also excluded slag-based materials from the table as possible carcinogens.
Also, pay attention to the heat capacity of materials. There is an opinion that the walls and floor of the house should be made of heat-intensive materials to get a comfortable indoor climate. There is too much misunderstanding. If heat-absorbing materials absorb free heat, such as from the sun, it has a positive effect on home insulation. Still, if they drink kilojoules generated by your furnace, they cause higher heating bills and have little impact on a comfortable temperature.
Material | Density, кг/м3 | Thermal conductivity, Watt/(м·град) | Heat capacity, Дж/(кг·град) |
---|---|---|---|
Aluminum | 2600 | 221 | 897 |
Fibrous asbestos | 470 | 0.16 | 1050 |
Asbestos-cement sheet | 1600 | 0.4 | 1500 |
Asbestos-rich asbestos sheeting | 1800 | 0.17…0.35 | — |
Asbestos-coated asbestos with 10-50% asbestos | 1800 | 0.64…0.52 | — |
Asbestos cement felt | 144 | 0.078 | — |
Asphalt | 1100…2110 | 0.7 | 1700…2100 |
Asphalt Concrete | 2100 | 1.05 | 1680 |
Aerogel (Aspen aerogels) | 110…200 | 0.014…0.021 | 700 |
Basalt | 2600…3000 | 3.5 | 850 |
Bakelite | 1250 | 0.23 | — |
Birch | 510…770 | 0.15 | 1250 |
Concrete on gravel or crushed stone of natural stone | 2400 | 1.51 | 840 |
Concrete on stone rubble | 2200…2500 | 0.9…1.5 | — |
Concrete on sand | 1800…2500 | 0.7 | 710 |
Dense silicate concrete | 1800 | 0.81 | 880 |
Thermal insulation concrete | 500 | 0.18 | — |
Petroleum bitumens for construction and roofing | 1000…1400 | 0.17…0.27 | 1680 |
Aerated concrete block | 400…800 | 0.15…0.3 | — |
Ceramic porous block | — | 0.2 | — |
Paper | 700…1150 | 0.14 | 1090…1500 |
Booth | 1800…2000 | 0.73…0.98 | — |
Mineral light wool | 50 | 0.045 | 920 |
Heavy mineral wool | 100…150 | 0.055 | 920 |
Vermiculite (in the form of bulk granules) | 100…200 | 0.064…0.076 | 840 |
Expanded vermiculite - backfill | 100…200 | 0.064…0.074 | 840 |
Vermiculite Concrete | 300…800 | 0.08…0.21 | 840 |
Air dry at 20°C | 1.205 | 0.0259 | 1005 |
Gas and foam concrete, gas and cellular concrete | 280…1000 | 0.07…0.21 | 840 |
Dry molded gypsum | 1100…1800 | 0.43 | 1050 |
Drywall | 500…900 | 0.12…0.2 | 950 |
Gypsoperlite mortar | — | 0.14 | — |
Normal clay | 1600…2900 | 0.7…0.9 | 750 |
Refractory clay | 1800 | 1.04 | 800 |
Gravel (filler) | 1850 | 0.4…0.93 | 850 |
Keramsite gravel - backfill | 200…800 | 0.1…0.18 | 840 |
Shungisite gravel - backfill | 400…800 | 0.11…0.16 | 840 |
Granite (facing) | 2600…3000 | 3.5 | 880 |
Earthy soil 10% water | — | 1.75 | — |
Earthy soil 20% water | 1700 | 2.1 | — |
Sandy soil | — | 1.16 | 900 |
Ground dry | 1500 | 0.4 | 850 |
Tamped down soil | — | 1.05 | — |
Oak material along the fibers | 700 | 0.23 | 2300 |
Oak across the fibers | 700 | 0.1 | 2300 |
Duralumin | 2700…2800 | 120…170 | 920 |
Iron | 7870 | 70…80 | 450 |
Reinforced Concrete | 2500 | 1.7 | 840 |
Limestone (facing) | 1400…2000 | 0.5…0.93 | 850…920 |
Products of expanded perlite on bituminous binder | 300…400 | 0.067…0.11 | 1680 |
Foam concrete products | 400…500 | 0.19…0.22 | — |
Ceramic porous stone Brauer 14.3 NF and 10.7 NF | 810…840 | 0.14…0.185 | — |
Hollow blocks of lightweight concrete | 500…1200 | 0.29…0.6 | — |
Full-bodied stones of lightweight concrete DIN 18152 | 500…2000 | 0.32…0.99 | — |
Building stone | 2200 | 1.4 | 920 |
Asbestos insulating cardboard | 720…900 | 0.11…0.21 | — |
Corrugated cardboard | 700 | 0.06…0.07 | 1150 |
Dense cardboard | 600…900 | 0.1…0.23 | 1200 |
Cork cardboard | 145 | 0.042 | — |
Cardboard construction multilayer | 650 | 0.13 | 2390 |
Insulating cardboard | 500 | 0.04…0.06 | — |
Foam rubber | 82 | 0.033 | — |
Natural rubber | 910 | 0.18 | 1400 |
Red cedar | 500…570 | 0.095 | — |
Keramsite | 800…1000 | 0.16…0.2 | 750 |
Clay peas | 900…1500 | 0.17…0.32 | 750 |
Playdate lightweight | 500…1200 | 0.18…0.46 | — |
Playdate concrete on playdate sand and expanded claydite concrete | 500…1800 | 0.14…0.66 | 840 |
Playdate concrete on perlite sand | 800…1000 | 0.22…0.28 | 840 |
Ceramics | 1700…2300 | 1.5 | — |
Blast furnace brick (refractory) | 1000…2000 | 0.5…0.8 | — |
Dense red brick | 1700…2100 | 0.67 | 840…880 |
Red porous brick | 1500 | 0.44 | — |
Clinker brick | 1800…2000 | 0.8…1.6 | — |
Facing brick | 1800 | 0.93 | 880 |
Hollow bricks | — | 0.44 | — |
Silicate Brick with Technical Cavities | — | 0.7 | — |
Silicate Slotted Brick | — | 0.4 | — |
Building Bricks | 800…1500 | 0.23…0.3 | 800 |
Masonry of medium-density stones | 2000 | 1.35 | 880 |
Gas silicate masonry | 630…820 | 0.26…0.34 | 880 |
Masonry of gas silicate heat insulation boards | 540 | 0.24 | 880 |
Masonry of standard clay bricks on cement-perlite mortar | 1600 | 0.47 | 880 |
Masonry of standard clay bricks on cement-sand mortar | 1800 | 0.56 | 880 |
Masonry of ceramic hollow bricks on cement-sand mortar | 1000…1400 | 0.35…0.47 | 880 |
Masonry of small bricks | 1730 | 0.8 | 880 |
Masonry of hollow wall blocks | 1220…1460 | 0.5…0.65 | 880 |
Masonry of silicate 11 hollow bricks on cement-sand mortar | 1500 | 0.64 | 880 |
Masonry of silicate 14 hollow bricks on cement-sand mortar | 1400 | 0.52 | 880 |
Masonry of sand-lime bricks on cement-sand mortar | 1800 | 0.7 | 880 |
Masonry of cellular bricks | 1300 | 0.5 | 880 |
Maple | 620…750 | 0.19 | — |
Oil paint (enamel) | 1030…2045 | 0.18…0.4 | 650…2000 |
Ice -20°C | 920 | 2.44 | 1950 |
Ice 0°C | 917 | 2.21 | 2150 |
Linoleum polyvinylchloride multilayer | 1600…1800 | 0.33…0.38 | 1470 |
Polyvinylchloride linoleum on a fabric backing | 1400…1800 | 0.23…0.35 | 1470 |
Lime, (15% moisture content) | 320…650 | 0.15 | — |
Larch | 670 | 0.13 | — |
Asbestos-cement flat sheets | 1600…1800 | 0.23…0.35 | 840 |
Gypsum cladding sheets (dry plaster) | 800 | 0.15 | 840 |
Cork lightweight sheets | 220 | 0.035 | — |
Mats, basalt wool sheets | 25…80 | 0.03…0.04 | — |
Mineral wool and synthetic binding mats | 50…125 | 0.048…0.056 | 840 |
MBOR-5, MBOR-5F, MBOR-C-5, MBOR-C2-5, MBOR-B-5 | 100…150 | 0.038 | — |
Chalk | 1800…2800 | 0.8…2.2 | 800…880 |
Copper | 8500 | 407 | 420 |
Marble (facing) | 2800 | 2.9 | 880 |
Deck flooring | 630 | 0.21 | 1100 |
Sawdust wood | 200…400 | 0.07…0.093 | — |
Hemp | 150 | 0.05 | 2300 |
Gypsum wall panels DIN 1863 | 600…900 | 0.29…0.41 | — |
Oak parquet | 1800 | 0.42 | 1100 |
Parquet piece | 1150 | 0.23 | 880 |
Panelboard parquet | 700 | 0.17 | 880 |
Foam Concrete | 300…1250 | 0.12…0.35 | 840 |
Foam PS-1 | 100 | 0.037 | — |
Foam plastic PS-4 | 70 | 0.04 | — |
Foam PVC-1 | 65…125 | 0.031…0.052 | 1260 |
Reopen FRP-1 foam | 65…110 | 0.041…0.043 | — |
Styrofoam | 40 | 0.038 | 1340 |
Styrofoam | 100…150 | 0.041…0.05 | 1340 |
Styrofoam People | 22…47 | 0.03…0.036 | 1600 |
Polyurethane foam | 40…80 | 0.029…0.041 | 1470 |
Polyurethane foam sheets | 150 | 0.035…0.04 | — |
Polyethylene foam | — | 0.035…0.05 | — |
Polyurethane foam panels | — | 0.025 | — |
Lightweight foam glass | 100..200 | 0.045…0.07 | — |
Foamed glass or gas-glass | 200…400 | 0.07…0.11 | 840 |
FoamFoil | 44…74 | 0.037…0.039 | — |
Parchment | — | 0.071 | — |
Pergamon | 600 | 0.17 | 1680 |
Reinforced ceramic slab with concrete filling without plaster | 1100…1300 | 0.7 | 850 |
Reinforced concrete elements ceiling with plastering | 1550 | 1.2 | 860 |
Monolithic flat reinforced concrete slab | 2400 | 1.55 | 840 |
Perlite | 200 | 0.05 | — |
Perlite bloated | 100 | 0.06 | — |
Sand 0% moisture | 1500 | 0.33 | 800 |
Sand 10% moisture | — | 0.97 | — |
Sand 20% moisture | — | 1.33 | — |
Sand for construction works | 1600 | 0.35 | 840 |
Fine river sand | 1500 | 0.3…0.35 | 700…840 |
Burnt Sandstone | 1900…2700 | 1.5 | — |
Fir | 450…550 | 0.1…0.26 | 2700 |
Pressed paper board | 600 | 0.07 | — |
Corkboard | 80…500 | 0.043…0.055 | 1850 |
Tile facing, tile | 2000 | 1.05 | — |
Alabaster slabs | — | 0.47 | 750 |
Gypsum slabs | 1000…1200 | 0.23…0.35 | 840 |
Fiberboard and chipboard | 200…1000 | 0.06…0.15 | 2300 |
Kersmith concrete slabs | 400…600 | 0.23 | — |
Polystyrene concrete slabs | 200…300 | 0.082 | — |
Glass staple fiber synthetic binder boards | 50 | 0.056 | 840 |
Cellular concrete slabs | 350…400 | 0.093…0.104 | — |
Flax-bark insulation boards | 250 | 0.054 | 2300 |
Bitumen-bonded mineral wool slabs, grade 200 | 150…200 | 0.058 | — |
Synthetic-binder mineral wool slabs, grade 200 | 225 | 0.054 | — |
Mineral wool boards with increased rigidity | 200 | 0.052 | 840 |
Organophosphate-bonded mineral wool boards with increased rigidity | 200 | 0.064 | 840 |
Starchbonded semi-rigid mineral wool boards | 125…200 | 0.056…0.07 | 840 |
Soft, semi-rigid, and rigid mineral wool boards on synthetic and bituminous binding | 50…350 | 0.048…0.091 | 840 |
Unpressed expanded polystyrene boards | 30…35 | 0.038 | — |
Styrofoam boards (extrusion) | 32 | 0.029 | — |
Porous concrete building slabs | 500…800 | 0.22…0.29 | — |
Fiberboard and fiberboard on Portland cement | 300…800 | 0.07…0.16 | 2300 |
Carpeting | 630 | 0.2 | 1100 |
Covering synthetic (PVC) | 1500 | 0.23 | — |
Gypsum seamless floor | 750 | 0.22 | 800 |
Polyvinyl chloride (PVC) | 1400…1600 | 0.15…0.2 | — |
Polycarbonate (Teflon) | 1200 | 0.16 | 1100 |
Polypropylene | 900…910 | 0.16…0.22 | 1930 |
Polystyrene UPP1, PPS | 1025 | 0.09…0.14 | 900 |
Polystyrene Concrete | 150…600 | 0.052…0.145 | 1060 |
Polystyrene concrete modified on the composite low-clinker binder in-wall blocks and slabs | 200…500 | 0.052…0.105 | 1060 |
Polystyrene concrete modified monolithic on Portland cement | 250…300 | 0.075…0.085 | 1060 |
Polyurethane | 1200 | 0.32 | — |
Polychlorvinyl | 1290…1650 | 0.15 | 1130…1200 |
High-Density Polyethylene | 955 | 0.35…0.48 | 1900…2300 |
Low-Density Polyethylene | 920 | 0.25…0.34 | 1700 |
Technical granulated cork | 45 | 0.038 | 1800 |
Bitumen-based mineral cork | 270…350 | 0.073…0.096 | — |
Cork flooring | 540 | 0.078 | — |
Coquina | 1000…1800 | 0.27…0.63 | 835 |
Gypsoperlite mortar | 600 | 0.14 | 840 |
Lime Mortar | 1650 | 0.85 | 920 |
Lime-sand mortar | 1400…1600 | 0.78 | 840 |
Lightweight mortar LM21, LM36 | 700…1000 | 0.21…0.36 | — |
Complex mortar (sand, lime, cement) | 1700 | 0.52 | 840 |
Cement-sand mortar | 1800…2000 | 0.6…1.2 | 840 |
Cement-perlite mortar | 800…1000 | 0.16…0.21 | 840 |
The rubber is soft. | — | 0.13…0.16 | 1380 |
Hard ordinary rubber | 900…1200 | 0.16…0.23 | 1350…1400 |
Rubber is porous | 160…580 | 0.05…0.17 | 2050 |
Ruberoid | 600 | 0.17 | 1680 |
Slate | 2600…3300 | 0.7…4.8 | — |
Mica puffed | 100 | 0.07 | — |
Mica across layers | 2600…3200 | 0.46…0.58 | 880 |
Mica, along with the layers | 2700…3200 | 3.4 | 880 |
Freshly fallen snow | 120…200 | 0.1…0.15 | 2090 |
Snow lying at 0°C | 400…560 | 0.5 | 2100 |
Pine and spruce along the fibers | 500 | 0.18 | 2300 |
Pine and spruce across the fiber | 500 | 0.09 | 2300 |
Pine resin 15% moisture | 600…750 | 0.15…0.23 | 2700 |
Reinforcing bar steel | 7850 | 58 | 482 |
Window glass | 2500 | 0.76 | 840 |
Glasswool | 155…200 | 0.03 | 800 |
Fiberglass | 1700…2000 | 0.04 | 840 |
Fiberglass | 1800 | 0.23 | 800 |
Glass fiberboard | 1600…1900 | 0.3…0.37 | — |
Pressed wood chips | 800 | 0.12…0.15 | 1080 |
Tol | 600 | 0.17 | 1680 |
Poplar | 350…500 | 0.17 | — |
Peat Pellets | 275…350 | 0.1…0.12 | 2100 |
Tuff (cladding) | 1000…2000 | 0.21…0.76 | 750…880 |
Tuphobeton | 1200…1800 | 0.29…0.64 | 840 |
Plywood | 600 | 0.12…0.18 | 2300…2500 |
Fibreboard (GreenBoard) | 450 | 0.063 | 2100 |
Cellophane | — | 0.1 | — |
Cement boards | — | 1.92 | — |
Concrete tiles | 2100 | 1.1 | — |
Clay tile | 1900 | 0.85 | — |
PVC asbestos tiles | 2000 | 0.85 | — |
Plaster gypsum | 800 | 0.3 | 840 |
Lime plaster | 1600 | 0.7 | 950 |
Synthetic resin plaster | 1100 | 0.7 | — |
Plastering with polystyrene mortar | 300 | 0.1 | 1200 |
Perlite plaster | 350…800 | 0.13…0.9 | 1130 |
Dry plaster | — | 0.21 | — |
Insulating plaster | 500 | 0.2 | — |
Facade plaster with polymer additives | 1800 | 1 | 880 |
Cement plaster | — | 0.9 | — |
Cement-sand plaster | 1800 | 1.2 | — |
Crushed stone and perlite sand - backfill | 200…600 | 0.064…0.11 | 840 |
Ebonite blew up | 640 | 0.032 | — |
Ecowool | 35…60 | 0.032…0.041 | 2300 |
Ansonia (pressed cardboard) | 400…500 | 0.1…0.11 | — |
Comparison of the thermal conductivity and heat capacity of a single-layer masonry of aerated concrete and a frame wall
One sq.m. wall of a single-layer masonry gas silicate 400 mm thick has a heat capacity of 228800 J / ha, and one sq.m. frame wall thickness of 176 mm 61548 J / ha (fiberboard 14 mm, 150 mm frame with eco wool, gypsum board 12 mm). The heat capacity of the aerated concrete walls is four times higher than that of framed walls, BUT... Let's take a conditional house 10h10h2, 5 m; the surface area will be 300 sq m and the volume of 250 cubic meters. In winter, when the street is -20 ° C, and you need the house was +20 ° C. Let's assume that you have a boiler with a capacity of 20kWh or 72000kJ. Let's omit the fact that the boiler first heats the water carrier, it passes through the pipes, warms them, and they, in their turn, give the heat to the surrounding air. Using convection, the air will be heated in the whole house in 10 minutes, but it will heat the surfaces of walls, floor, and ceiling, and that is why the air temperature will not be 20°Ñ in 10 minutes. The air will give its heat to the plaster. In the whole house, Cement-sand plaster with a thickness of 10 mm weighs 4800 kg and can accumulate heat 51 kWh. Therefore, it takes 2.7 hours to heat the dressing to 20 degrees and all the air in the house. But during this time, the application will give 227 watts to the gas concrete, which needs much more heat to heat to 20 degrees. The thermal resistance of the plaster of the whole boiler consumes 9152000 J x 0.000277778 W/h x 300 m² = 762.6 kWh to heat the building envelope of the gas concrete house + 3.36 kWh of air and lose 344.7kW. 775 kWh.
To heat 1 square meter of the frame wall, the boiler will expend 61548 J x 0.000277778Wh= 17.1Wh +3.36kWh and lose 3.6kWh 24kWh. In other words, a 20kWh boiler will require about
This means that your heating boiler will work longer to heat the room to a comfortable temperature because it will heat the air and the walls, but while the walls will be heated, they will also cool, giving the heat to the street. Following the Fourier heat conduction law, the flow of heat transfer will be directed towards the hard road. Your mother must have told you more than once as a child: "Don't sit on a concrete floor, sit on a bench." Because concrete takes heat from the body, and a person can catch a cold. That's why all seats are made of wood or other poorly heat-transferring materials.
The heat loss through the wall can be calculated according to the formula:
[W/(m-K) - (m2-K)/m = W/(m-K) - (m-K) = W].
Each square meter of gas silicate masonry at a temperature difference of 40° will leak 30Wh. At the same heat loss through the frame wall, the thickness of 150 mm will be 12W / hour. The south wall of the house of aerated concrete on a hot day is more heated by the sun than the frame wall and gives all the heat into the room, so in the summer, in a house made of aerated concrete hotter.
Heat capacity is essential in the heat carrier and the floor. If you need heat capacity in a frame house, make a "warm floor."
Therefore, gentlemen, build a house on frame technology. There will be you, and high thermal resistance and sufficient heat capacity or, in simple terms, the place will be warm and comfortable.