Insulating Concrete Form system combines two well-established building products. These products - reinforced concrete and expanded polystyrene. Reinforced concrete gives strength and durability. Expanded polystyrene (EPS) insulation - energy efficiency. ICFs are made up of two layers of rigid insulation held together with ties. This insulation forms ICF form units with a cavity in the center. Builders stack the ICF form units in the shape of the wall. After they add reinforcing steel into the form's cavity and then place concrete into the form. The result is a reinforced concrete wall with a layer of insulation on each side.
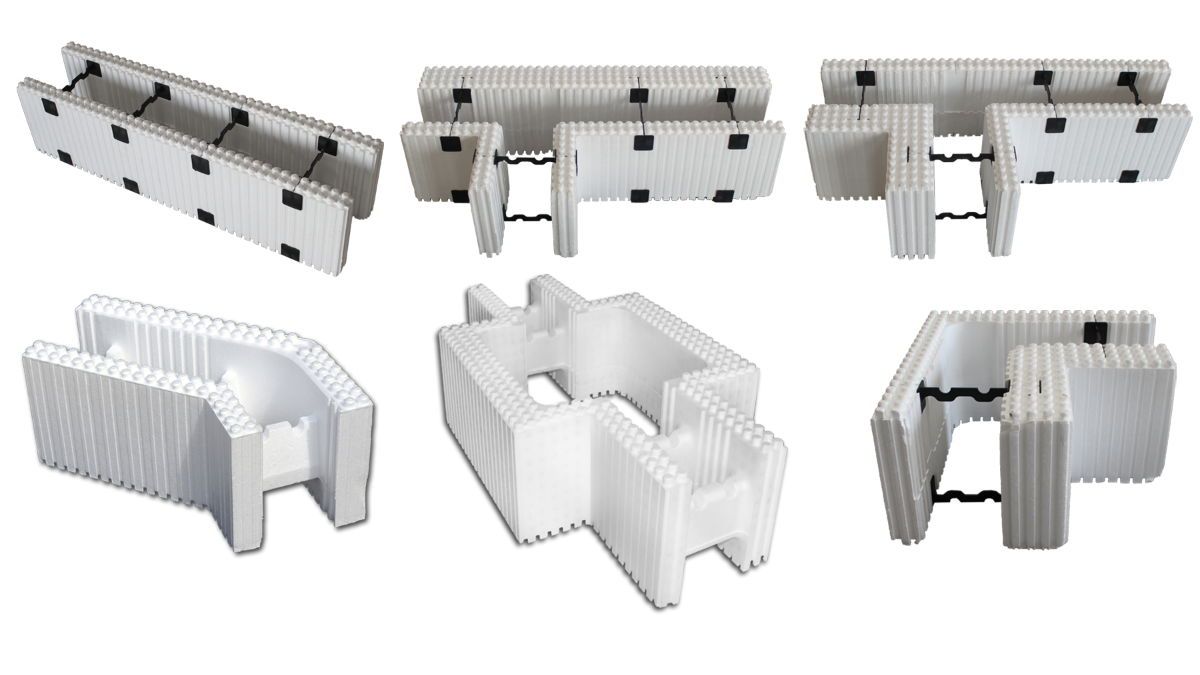
What makes ICFs different than traditional concrete construction?
Insulating Concrete forms remain in place after the concrete is cured. This system provides an ideal load-bearing wall, thermal envelope, fire barrier, and sound barrier.
Besides to ICF walls, there are also ICF concrete floor and roof systems. The concept is like the ICF wall. A slab is made with rigid insulation to function as a one-sided form at the bottom surface. The forms are installed to span between concrete walls, reinforcing steel is placed and then concrete is placed over the forms. The result is a reinforced concrete floor or roof with rigid insulation on the bottom.
ICF wall systems are suitable for single-story buildings to 20+ story high-rise buildings. There are examples of ICF buildings all over the world. Schools built with ICF are popular due to low- or net-zero energy use. Theaters are also trending towards ICF construction for superior sound attenuation.
What makes ICFs so attractive for construction?
They are cost-competitive with masonry construction. An owner gets a building that is disaster resilient and energy-efficient at the same cost. Fire safety is a key element of construction. Occupants sleep in these buildings and are challenged to evacuate during a fire. Concrete walls and floors provide the fire resistance needed to contain the fire within a single unit. Concrete walls and floors imposing less risk to firefighters and property.
ICF wall units are comprised of large molded EPS blocks, like Lego® blocks with a cavity for concrete in the center. The blocks range in size from 48 to 96 inches long and 12 to 24 inches high depending on the manufacturer. The most common configuration of an ICF unit consists of two layers of 2-3/8- to 2-5/8-inch-thick EPS spaced 4, 6, 8, 10 or 12 inches apart. The most common cavity is 6 inches or 8 inches for most low to mid-rise buildings. For taller buildings, taller walls, or large loadings, thicker walls are necessary. For simplicity, ICFs are generally called out by the width of the cavity. For example, an ICF with a 6-inch cavity we call a 6-inch ICF.
ICF Wall Systems
The blocks are designed to have interlocking teeth that hold the forms together. Most manufacturers supply straight blocks, corner blocks, angled blocks, t-blocks and some have curved blocks. Most even provide special blocks with brick ledges. Many companies supply blocks that are fully assembled and ready for installation. Some ship blocks that are folded into a flat configuration and then unfolded for installation. One manufacturer ships blocks and ties separately that builders assemble on site. Many have a special window and door bucks. Some provide bracing, clamps and scaffolding to make the construction process more efficient.
There are some ICF forming systems that are made of other insulating materials. For example, they use wood composite panels instead of the inner EPS layer. But flat-wall ICF systems dominate the marketplace. Because ICF Flat blocks are designed to create standard structural elements using conventional design methods.
There are at least a dozen companies that manufacture flat-wall ICF systems. They can deliver their product throughout the U.S. and Canada.
EPS insulation used for ICFs is governed by ASTM C 578, Type II closed-cell foam with an R-value of 4 per inch. Polystyrene beads are first expanded with steam forming high-density beads, which are injected into a mold to form the desired shape. Once removed from the molds and cured, EPS is a stable and durable material ideal for construction. Chlorofluorocarbons (CFCs), hydrofluorocarbons (HFCs) or formaldehyde are not used in production, so there is no off-gas emission. EPS is moisture resistant, non-absorbent and resistant to mold and rot. EPS contains a flame retardant and the smoke from burning is non-toxic. Besides, EPS is recyclable at its end of life.
The plastic ties that hold the two wythes of the block together are as a rule made with polypropylene plastic. They are designed to withstand the liquid concrete pressure during construction. Ties have notches that secure horizontal and vertical reinforcing bars to minimize the need to use tie wire. The ties have no thermal bridging, they do not degrade or rot over time. All ties have furring strips embedded in the EPS for screw-on attachment of exterior or interior finishes.
Reinforcing steel used in ICF walls is the same used for any other type of concrete structure. Typically, smaller diameter bars are used such as #4, #5 or # 6, but thicker bars can be used for higher loading, concentrated loads and pilasters. For 6-inch or 8-inch ICFs, reinforcing steel is placed in one layer in the center of the wall at wide spacing. For 10-inch and larger ICFs, one can consider using 2 layers of reinforcing on each face. The goal is to minimize congestion and ease concrete placement. In some cases, steel fibers have been used in place of reinforcing steel in ICF walls. Most common applications use both horizontal and vertical steel reinforcement.
Concrete is typically placed in ICF walls using a boom-type concrete pump. Line-pumps or even conveyor belt equipment can be used too. Specified compressive strength used in ICF walls can be whatever is required to resist structural loading. The most common is a 3000 psi (21MPa) or 4000 psi (27.6 MPa) concrete pump mix. The recommended largest aggregate size should be ½-inch for 4- and 6-inch cavity forms and ¾-inch for 8-inch and larger cavity forms. The required concrete slump is 6 inches. To accommodate pumping using high-range plasticizers and mid-range water, the slump could be up to 8 inches or more.
Concrete is generally placed one level at a time. In other words, ICF blocks are stacked in the shape of the wall for a single story. Reinforcing steel is installed as the forms are stacked. Bracing, scaffolding, window and door bucks are installed. Once the ICF wall is plumbed and straight, concrete can be placed in 4-foot lifts. For a wall that is 12 feet tall, concrete would be placed in 3 different lifts by placing 4 feet of concrete at one time for the entire length of the wall. By the time the pump reaches the starting point, the concrete is usually stiff enough to place the second lift and so on.
Electrical and plumbing lines can be embedded into the interior layer of foam. To do this, the builders cut channels with a hot-knife or other tool. Interior or exterior finishes can be applied directly to the surface by screwing into the plastic furring strips. Almost any finish can be applied to ICF. Gypsum board on the interior and stucco, brick or siding on the exterior are common finishes suited to ICF construction.
Any house plan on our website can be changed to an ICF house for a reasonable fee.