Foam block for house construction
Foam blocks
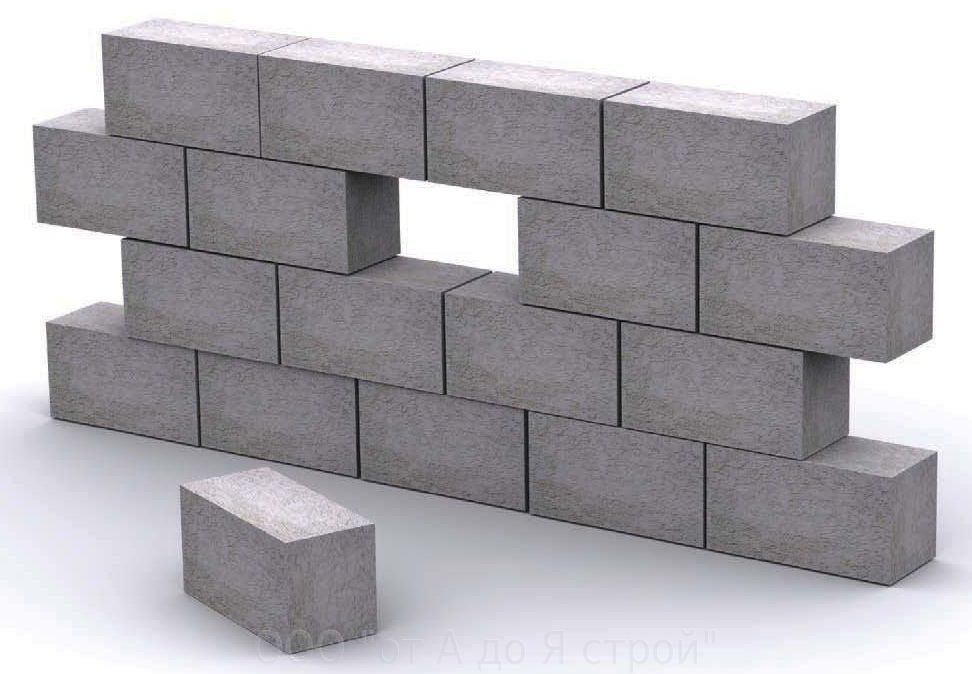
What if you have chosen the house plan of foam blocks, and you are satisfied with everything, and the layout and facade, it remains only to confirm your confidence that the walls of foam blocks are able to meet the requirements of seismicity and climatic conditions of your region. The rest rests on the conscience of the producers of materials and builders.
In this article, we will briefly consider the composition and technology of the production of foam blocks to understand the physics of the foam block as a building material.
Styrofoam block composition
The cellular properties of the foam block allow it to be relatively strong and have low thermal conductivity. These qualities are achieved thanks to the composition, which includes
1. Cement.
2. Sand with a fraction of at least 5 mm.
3. Water.
4. Foamer.
5. Reinforcing fibers
If the first three components are clear to us, then 4 and 5 points need to be analyzed in detail, because that is where the effectiveness of our unit.
Types of blowing agents
The blowing agent is used to form pores in the foam block, giving it energy-efficient properties.
In the market of building materials, there are foam-formers of three kinds: protein glued and synthetic. Each of them meets the necessary characteristics, but are acceptable. only for its method of foaming. Protein consists of protein derived from animal and vegetable raw materials. Gluten rosin by washing the wood resin.
Synthetic
thanks to the development of synthetic materials. If protein and glutinous foaming agents are mechanically foamed before being added to the main mixture (in foam generators), synthetic ones are mandatorily prepared in special turbulent baroque chambers, because only there they reach the required characteristics (stability, viscosity).
Reinforcing fiber
When adding reinforcing fibers (fibers), up to 20% increases the strength of the foam block and improves its performance.
Glass fiber, as a reinforcing material, is popular in the production of foam blocks, due to its low cost. Other fibers based on polypropylene and basalt are more expensive, in addition to the above, are binder modifiers at the micro-level.
Physical properties of the foam block, such as shrinkage, microcracks, and, what is very important, the presence of defects during decomposition and transportation, directly depend on the quality of the selected and used reinforcing fibers.
Production technology of foam blocks
In a carefully mixed mixture of sand, cement, arm fiber, and water add a prepared foaming agent. Then the whole solution is poured into molds (casting method), which are pre-lubricated with special greases. Some manufacturers save money using a variety of oiled waste, which leads to spillage of the corners of the block during demolding.
After 16-18 hours the blocks are unpacked and sent to stand for another 48 hours until they are fully ready. In all processes, the temperature in the room is not less than 20 º C.
It is important to note that with the addition of hardeners, the residence time is reduced according to the recommendations for use.
It is obvious that this method of forming blocks has a very important unsatisfactory moment - bad geometry of the product, as the partitions of the cassettes made of the metal sheet when pouring the mixture deformed under the influence of uneven flow.
There is another approach to manufacturing, but it is expensive and it is not used by all manufacturers.
1) The use of quality forms of thick material,
where all dimensions are carefully calibrated and adjusted.
2. Formation of the layer into large forms with subsequent cutting
according to the size of blocks.
3. Drying of products in chambers at a temperature of 40-50 º C for 8 hours.
Result
The foam block when used to build a house has important features:
1. Low weight, with large dimensions, thus significantly increases productivity.
2. environmentally friendly - the composition of the foam block is completely harmless.
3. Resistant material to all kinds of fungi and mold.
4. Many years of service life.
5. The presence of high shrinkage - must apply reinforcement.
6. Water permeability - it is necessary to make facade systems.
7. Careful attitude during transportation and masonry - the material is fragile because of its structure.
Choose a good manufacturer of foam blocks and experienced builders and your home will serve you for many years without bringing problems in operation.
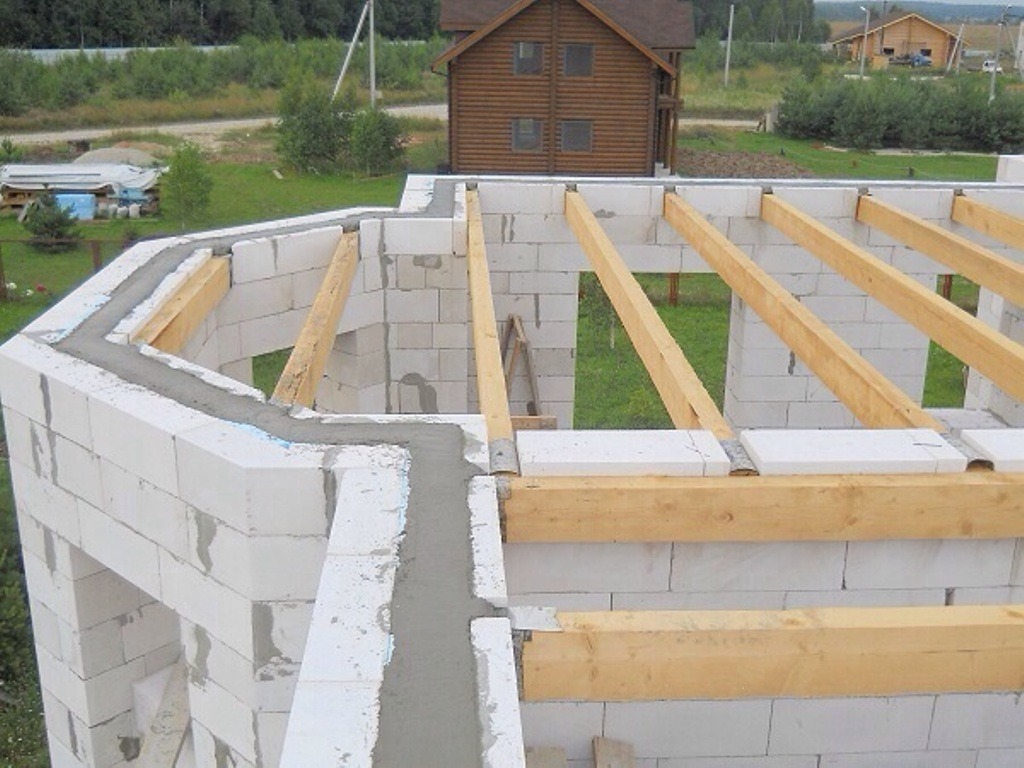